How Brass is Made: A Step-by-Step Guide
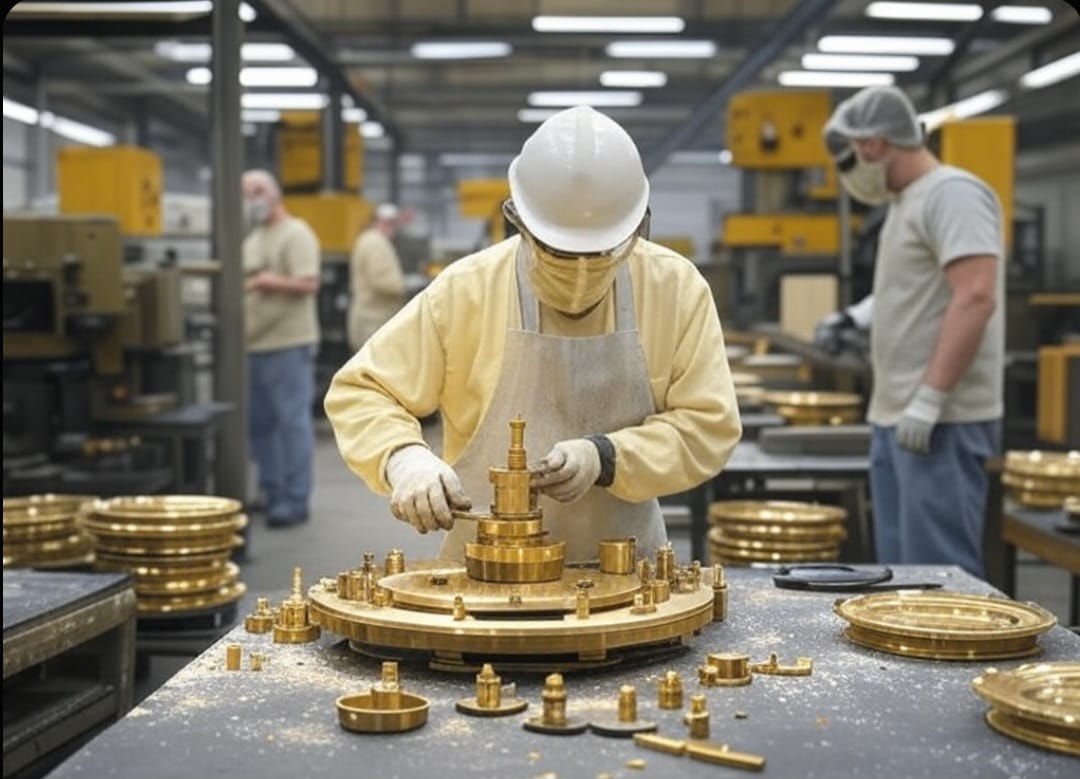
Brass is a versatile and widely used metal alloy, primarily composed of copper and zinc. Its unique combination of strength, corrosion resistance, and malleability makes it a popular choice for applications ranging from musical instruments to plumbing fittings. The process of making brass involves several key steps, blending science and craftsmanship. Below, I’ll walk you through how brass is made, from raw materials to the finished product.
Step 1: Gathering Raw Materials
The journey of brass begins with its two primary ingredients: copper and zinc. Copper is typically mined from the earth as copper ore, which is then refined into pure copper metal. Zinc, similarly, is extracted from zinc ore (like sphalerite) and processed into a usable form. The exact ratio of copper to zinc can vary depending on the desired properties of the brass—more copper results in a reddish hue and greater ductility, while more zinc increases strength and gives it a yellowish tone. Other metals, such as lead, tin, or aluminum, may also be added in small amounts to enhance specific characteristics, like machinability or corrosion resistance.
Step 2: Melting the Metals
Once the raw materials are prepared, the next step is melting. Copper, which has a higher melting point (around 1,083°C or 1,981°F), is typically melted first in a furnace. These furnaces are often gas-fired or electric and designed to handle high temperatures. Once the copper is fully molten, zinc is added to the mix. Zinc melts at a lower temperature (about 420°C or 788°F) and has a tendency to vaporize, so this step requires careful control to avoid losing too much zinc to evaporation. The molten metals are stirred to ensure a uniform mixture.
Step 3: Alloying and Adjusting Composition
After melting, the copper and zinc blend to form brass. The exact proportions are adjusted based on the type of brass being produced—for example, “cartridge brass” (70% copper, 30% zinc) or “yellow brass” (67% copper, 33% zinc). At this stage, any additional elements (like lead for improved machining) are introduced. The molten alloy is tested, often using spectrometry, to confirm the composition meets the required specifications. If adjustments are needed, more copper, zinc, or other metals are added.
Step 4: Casting the Brass
Once the alloy is ready, it’s poured into molds to solidify. This process, known as casting, can take different forms depending on the final product. For large-scale production, the molten brass might be poured into ingots or billets—large blocks or bars that can be further processed. Alternatively, it can be cast directly into shapes closer to the final product, such as sheets, rods, or tubes. The brass cools and hardens as it takes on the shape of the mold.
Step 5: Cooling and Solidification
After casting, the brass is allowed to cool at a controlled rate. Rapid cooling can create internal stresses or cracks, so this step is carefully managed. Once solidified, the brass is removed from the molds. At this point, it’s still rough and may contain imperfections like air bubbles or surface irregularities.
Step 6: Shaping and Finishing
The solidified brass is then shaped into its final form through various methods. These can include:
Rolling: Passing the brass through rollers to create thin sheets or plates.
Extrusion: Forcing the brass through a die to form rods, tubes, or complex profiles.
Forging: Heating and hammering the brass into specific shapes.
Machining: Cutting or drilling to refine the product.
After shaping, the brass undergoes finishing processes like polishing, grinding, or annealing (a heat treatment to relieve stress and improve workability). This enhances its appearance and ensures it meets the necessary tolerances.
Step 7: Quality Control and Testing
Before the brass is ready for use, it’s subjected to rigorous quality checks. These may include tests for hardness, tensile strength, and corrosion resistance, as well as visual inspections for surface defects. Only after passing these tests is the brass deemed ready for distribution or further manufacturing.
Brass production is a fascinating blend of metallurgy and precision, transforming raw copper and zinc into a material that’s both functional and beautiful. Whether it’s destined to become a trumpet, a door knob, or a bullet casing, the process ensures brass retains its signature durability and golden gleam.